Discover how Datwyler’s materials and components are transforming the performance of batteries to make electric vehicles fit for the future.
Every area of the automotive sector, from small vehicles to large trucks, is undergoing a fundamental transition, with every part of the power system being redesigned and redeveloped to make the important shift from fossil fuel to electric.
Of course, for this transition to be successful, the main focus of development has to be the battery. Its power, capacity, charging rate, size, weight, and safety are all vital factors in the overall performance of the vehicle, so companies are placing a huge amount of focus on this part of the vehicle.
As one of the world’s leading manufacturers of elastomer seals, Datwyler understands the key role these components have in battery systems, and how they make a significant difference to the performance, longevity, and safety of the battery. Our global team of experts are constantly developing new solutions to the challenges of the new generation of lithium-ion (Li-ion) batteries – here are just a few of those solutions.
Thermal interface materials (TIM)
One of the main challenges of Li-ion batteries for vehicles is thermal management. Used in electric vehicles for their relatively higher power and energy density, Li-ion batteries are highly attractive to manufacturers. However, there are certain drawbacks to these batteries, such as the risk of thermal runaway, as well as the challenge of the degradation of components such as electrolytes at higher temperatures. For safety and long-term performance, it is crucial that these batteries remain within a certain temperature range, something that thermal interface materials can help with.
Made of an elastomeric material with high heat conductivity, thermal interface materials are designed to evacuate heat efficiently from Li-ion batteries by reducing the contact thermal resistance. These unique materials are placed between battery cells and the cooling system in the form of conventional rubber pads, and can influence almost every aspect of a battery’s performance, from charging and discharging at high C-rates to controlling the temperature of batteries and preventing thermal runaway.
Right now, there is considerable interest in thermal interface materials, with battery and vehicle manufacturers keen to use the latest technologies to improve the performance and safety of battery systems. The ability of thermal interface materials to offer effective thermal management for batteries in a range of sizes and thicknesses – as well as low weight – is a compelling development, and samples are currently in production.
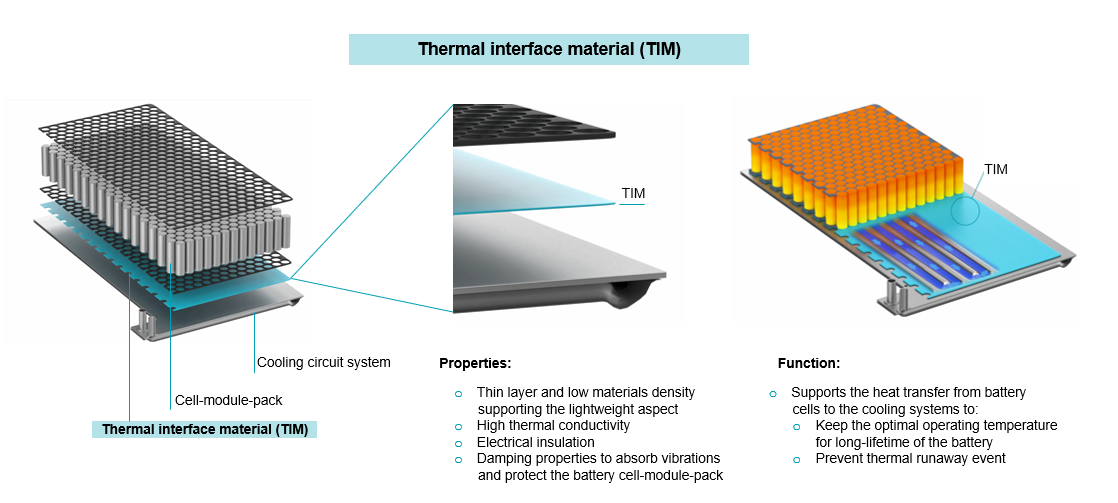