The battery cell market is currently in a period of innovation and growth, driven primarily by the electric vehicle (EV) sector's demand for higher energy density,
longer lifespan, and faster charging capabilities. Solid-state batteries have seen
significant advances, which promise higher safety and energy density, and the
integration of silicon anodes and lithium metal anodes to improve battery
performance. Additionally, there is a strong push towards sustainable and recyclable
battery materials to minimize environmental impact and reduce dependency on raw
materials with volatile supply chains.
It is one of the fastest-moving areas within the mobility sector, where rapid technological advancements, coupled with increasing investments from both private and governmental entities, are accelerating innovation cycles. Companies are under constant pressure to improve energy efficiency, reduce costs, and comply with stringent regulatory standards – for example UL94V0, which is the highest level of fflame retardancy – and PFAS free solutions which are governed by REACH. The
fast-paced nature of this market is further driven by the global race to dominate the EV market, with significant competition among leading manufacturers to deliver the most advanced and cost-effective battery solutions.
Selecting the best option
In terms of the batteries themselves, lithium Ion batteries present in different form factors – from cylindrical versions to prismatic options. The method of sealing these battery cells is critical as it directly impacts the battery's safety, performance, and longevity. Proper sealing prevents leakage of electrolytes, ingress of moisture, and exposure to external contaminants, all of which can lead to catastrophic failures, including fires or explosions.
Sealing also influences the mechanical stability and thermal management of the battery, which is essential for maintaining optimal performance under various operating conditions. Therefore, selecting the appropriate sealing method is paramount for ensuring the reliability and safety of battery cells. Various assembling and sealing methods are available, including bolting, laser
welding, and heat sealing, with each offering different advantages in terms of mechanical strength, sealing integrity, and manufacturability. For instance, laser welding provides a high-strength, hermetic seal ideal for high-performance applications, while heat sealing is often used for pouch cells due to its flexibility and cost-effectiveness. The choice of sealing method depends on the specific requirements of the battery application and the desired balance between performance, cost, and manufacturing complexity.
Benefit from material expertise and advanced capabilities
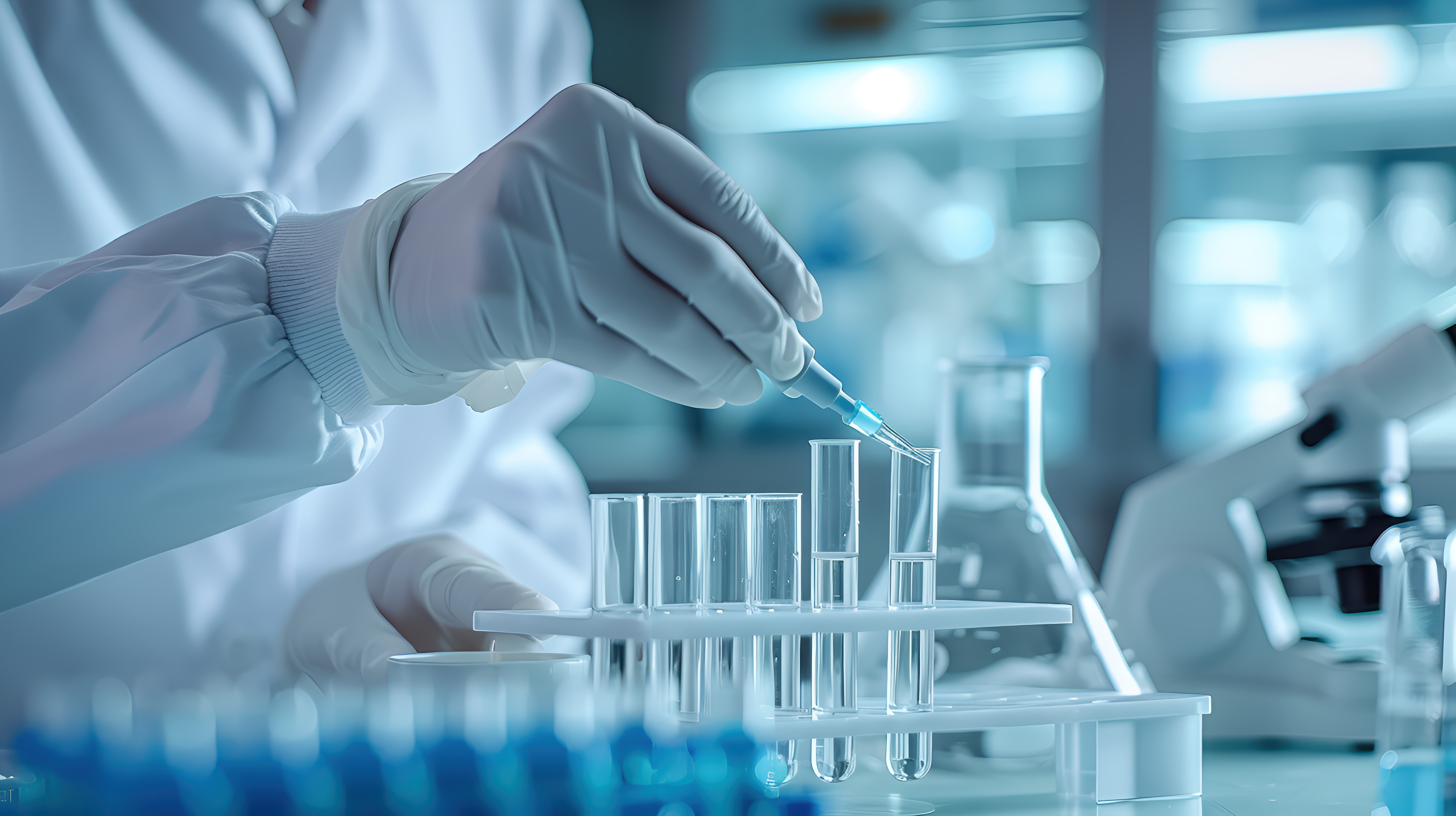
At Datwyler, we have developed advanced sealing solutions tailored to meet the stringent demands of the EV battery market. Leveraging our expertise in material science and precision manufacturing, we offer a range of innovative sealing materials and designs that enhance battery safety and performance. Our solutions include high-performance elastomers that provide superior resistance to chemicals,
temperature extremes, and mechanical stresses, ensuring robust and reliable seals for various battery configurations. We have screened several compounds and tested them thoroughly for their ability to
be in contact with corrosive electrolytes. We have also tested if any possible leachables from the material will impact the cell’s electrochemistry. Here, our deep understanding of material properties and extensive experience in the automotive sector, enables us to deliver customized sealing solutions that meet specific customer needs. We offer a comprehensive portfolio of sealing materials, including high-performance elastomers like FKM and EPDM, each optimized for different operating conditions.
Additionally, our advanced manufacturing capabilities ensure high precision and consistency, reducing the risk of seal failures and enhancing overall battery reliability. Currently, the most popular sealing solutions for cell seals are FKM (Fluoroelastomer) and certain thermoplastics. They have certain advantages such as high thermal resistance and chemical stability. However, many customers are now trying to replace FKM and thermoplastic materials with EPDM (Ethylene Propylene
Diene Monomer) due to cost savings and PFAS regulations. While FKM is known for its excellent chemical resistance and thermal stability, making it a popular choice for battery sealing, EPDM solutions developed by Datwyler experts offer a cost-effective alternative with good resistance to weathering, ozone, and a wide range of temperatures. EPDM is generally more affordable and
provides sufficient performance for many applications. Though it may not match the high-temperature resistance properties of FKM, EPDM is even better for contact with electrolytes in terms of swelling. High-performance sealing materials like FKM and EPDM contribute to the prevention
of leaks and contamination, which can cause battery failure or safety hazards. Balancing performance and cost with the appropriate material selection ensures competitive advantage and customer satisfaction.
Staying on track, ahead of the curve
The future of battery cell sealing is likely to see continued advancements in material science and sealing technologies. Innovations will focus on improving the performance characteristics of seals to meet the evolving demands of higher energy density batteries and faster charging systems. Sustainable materials and manufacturing processes will gain prominence, driven by environmental regulations and consumer preferences. Additionally, smart and adaptive sealing solutions that
can respond to real-time operating conditions may become a part of next-generation battery designs. At Datwyler we continue to advance our own capabilities and to further our expertise to ensure our customers stay ahead of the curve and deliver the safest, highest quality solutions to their customers.