Putting the design into Eco-design
Datwyler, a top elastomer parts manufacturer, is committed to environmental responsibility through 12 ESG focus areas. This includes a pledge to achieve climate neutrality by 2030 and initiatives for resource-friendly production, sustainable procurement, and Eco-design.
One of Datwyler’s key ESG (Environmental, Social, and Governance) focus topics is Eco-design, a unique sustainability concept that ensures the environment is at the heart of every aspect of product development.
As one of the world’s leading manufacturer of elastomer parts for the mobility sector, Datwyler has a strong sense of responsibility for the environment. We understand that our actions today will have an influence on climate change. Whatever we can do to minimise our impact and the impact of the automotive industry on the environment will improve the lives of billions around the world for generations to come.
At Datwyler, we take sustainability extremely seriously, which is why we established 12 Environmental, Social, and Governance (ESG) focus topics that outline our commitment to the environment and our customers, with measurable objectives and quantifiable key figures for effective monitoring. While the Social group of topics describes our responsibilities to our employees, our customers, and local communities, Governance details our transparency of reporting, compliance and ethics, and corporate commitment.
However, it is the topics within the Environmental group that have the most influence on climate change, topics that include our commitment to be climate neutral by 2030, as well as resource-friendly production, sustainable procurement, and Eco-design.
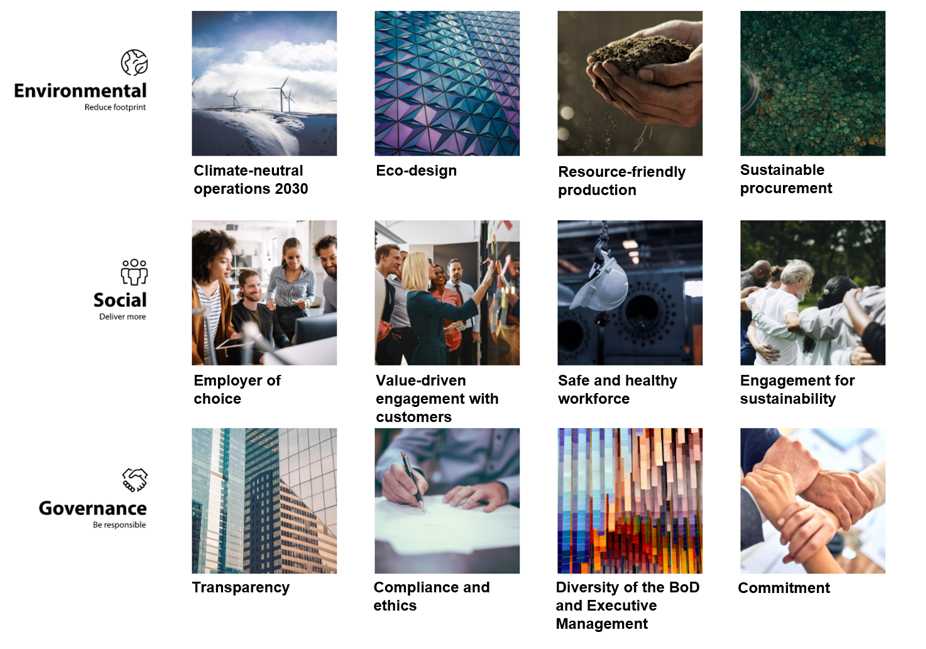
Eco-design is a unique sustainability approach that ensures that we consider the impact of our products on the environment at every stage of the development process. This involves looking closely at our three core competencies material know-how, solution design and operational excellence: everything from how raw materials are processed and transported to the efficiency of the manufacturing process and long-term reliability of the final product. Only by assessing the environmental impact of each stage can we gain a true picture of the sustainability of an individual product –information that we can pass on to our customers and suppliers to support with their environmental reporting and improve the sustainability of the whole supply chain.
One of the key stages in the life cycle of a product is design, and it is here that many of the key decisions are made that directly influence sustainability. Whether it is the choice of material, reducing the amount of waste, cutting energy consumption, or recycling scrap material for other uses, our design teams are constantly looking for ways to improve the efficiency of the entire production process.
It is this constant attention to detail and deep knowledge of materials and processes that is at the heart of the Eco-design principle. Investing such large amounts of time and resources into the design stage of all our parts results in high levels of efficiency at every other stage, reducing energy and waste while improving reliability.
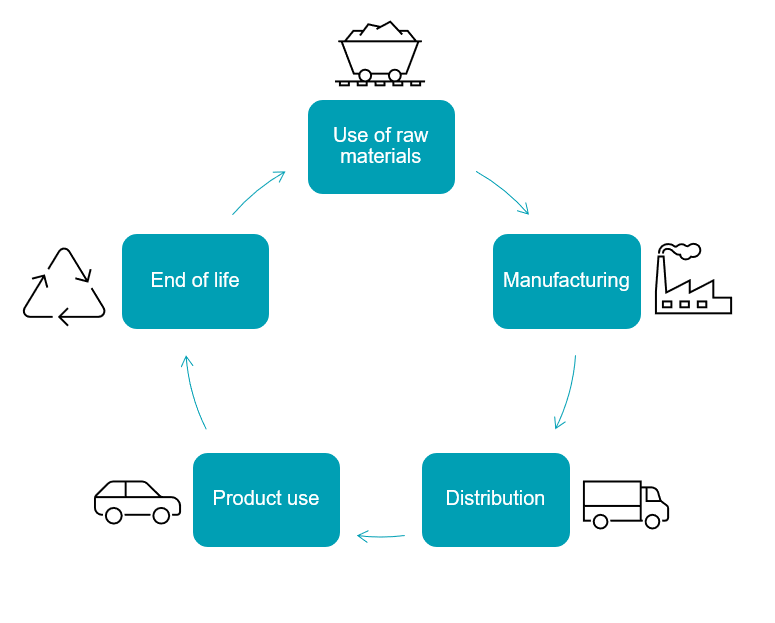